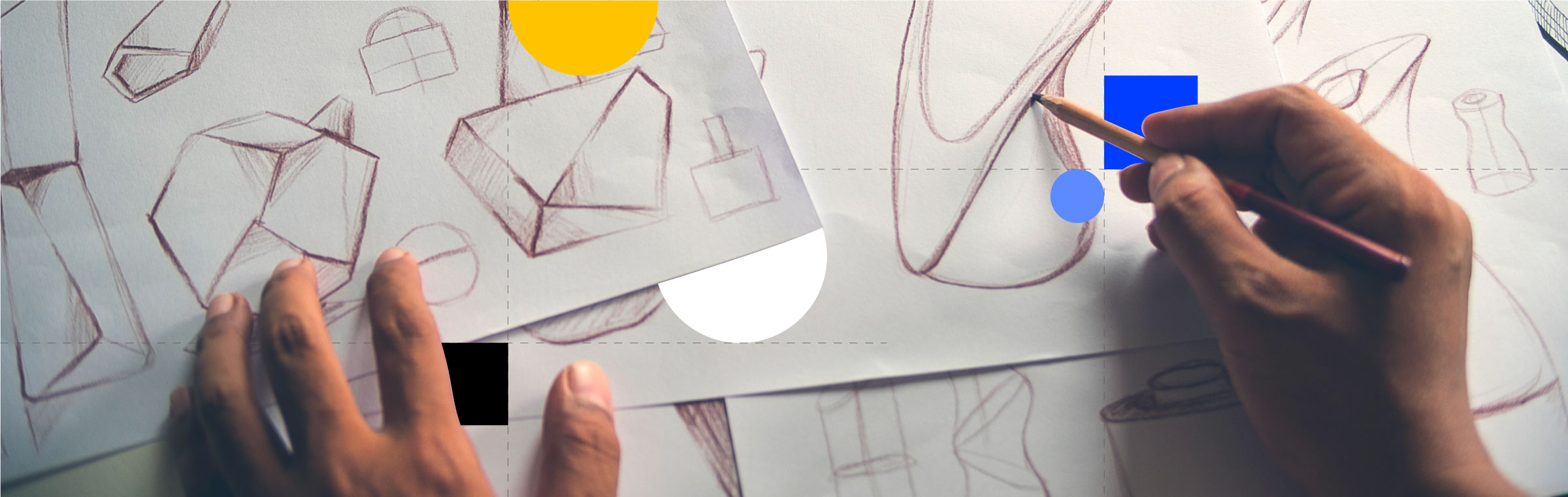
Design For Manufacturing
Design for Manufacturing can reduce time and costs while improving quality.
Feb 3, 2023
When it comes to product development, design and manufacturing go hand in hand. However, many companies make the mistake of focusing solely on the design stage without considering the manufacturing process. Failing to integrate the manufacturing side of the process can lead to increased costs, longer lead times, and even product failures. That's where Design for Manufacturing (DfM) comes in.
DfM focuses on designing products to make them easy and cost-effective to manufacture. It involves analyzing the manufacturing process from the start of the design phase to identify potential issues and optimize the design for manufacturing. By doing so, DfM can lead to reducing manufacturing costs and an overall improved product quality.
But DfM is not only about economics; it also positively impacts the environment. According to a National Renewable Energy Laboratory study, DfM can reduce material waste, energy consumption, and greenhouse gas emissions.
In this article, we'll take a closer look at what DfM is, its benefits, and why it matters. We'll also explore the different approaches to DfM, the steps involved in implementing it, and how to get a DfM session with a specialized engineer that will save you time and money.
What is Design for Manufacturing (DfM)
DfM is a methodology aiming to design manufacturing-friendly products. It's a systematic approach to assessing a product design process with the goal of making it easy and cost-effective to manufacture. This typically involves considering the materials, processes, and equipment used to manufacture a product and designing it to minimize the costs and complexity of the manufacturing process.
Design for Manufacturing can include techniques such as using standard components, reducing the number of fasteners, designing parts that are easy to handle and align during manufacturing, and so on. The process involves analyzing the manufacturing process from the start of the design phase to identify potential issues and optimize for the selected manufacturing process. DfM goals are:
Reducing material costs
Cut manufacturing expenses
Improving product quality
Shortening lead times
Increasing flexibility
Design for Manufacturability, Design for Assembly, and Design for Environment
There are several different approaches closely connected to DfM, and the best method will depend on the specific product and manufacturing process. Some of these include:
Design for Assembly (DfA)
DfA is a process used to optimize the design of a product to make its assembly as efficient and cost-effective as possible. DfA aims to minimize the number of parts, simplify the assembly process, and reduce the time and labor required to assemble the product.
Design for Manufacturability (DfMb)
DfMb is about designing parts, assemblies, and products that are easy to manufacture by considering the chosen manufacturing process and equipment. DfMb is about efficiency, repeatability, and low cost.
Design for Environment (DfE)
DfE is a holistic approach to product design that considers the entire lifecycle of a product, from the extraction of raw materials to the disposal of the product at the end of its useful life. The goal of DfE is to minimize the environmental impact of a product by reducing its resource consumption, pollution, and recyclability.
Design for Manufacturing Benefits
Companies, entrepreneurs, product managers, and even independent designers and engineers can benefit from correctly implementing DfM in their processes. The advantages are many and can include the following:
Cost savings: By designing products to make them easy to manufacture, DfM can lead to significant cost savings.
Quality improvement: By identifying potential issues early in the design process, DfM can help improve product quality.
Reduced lead time: By optimizing the design for manufacturing, DfM can help to make a more effective production process, reducing lead times.
Increased flexibility: By designing products to make them easy to manufacture, DfM can increase flexibility in the manufacturing process.
The Importance of DfM in Product Development
DfM is not only crucial for reducing production and labor costs and improving product quality, but it also plays a crucial role in a product's overall success and a company's competitiveness.
A study by the University of Cambridge found that companies implementing DfM are more likely to be successful in the long term than those going through longer, more iterative processes.
In today's fast-paced business world, time-to-market is crucial. DfM can help to reduce lead times, which means that products can be brought to market faster. A study by MIT found that reducing lead times by just one day can increase sales by up to 5%.
Implementing DfM in Your Product Development Process
Now that you understand the importance of DfM in product development, you may be wondering how to implement it in your process. Here are a few tips to get you started:
1. Start early
The earlier you start thinking about DfM, the better. It's much easier to adjust a design from the early stages before it reaches the final one, so try incorporating DfM into your product roadmap as early as possible.
2. Get input from the manufacturing team or partner
The manufacturer is the one that will be responsible for making the product, so it's essential to get their feedback on the design. They may have valuable insights into what will and won't work in manufacturing.
3. Test and optimize
Once you've incorporated DfM into your design process, testing and optimizing the design is essential. This will help you identify potential issues and make necessary changes.
4. Get help from experts
You can book a DfM session with experienced professionals. Wikifactory has a team of engineers experienced in DfM ready to help you improve the manufacturability of your product idea.
Incorporating DfM into your product development process can seem daunting at first. Still, with the right approach, it can be a straightforward process leading to significant cost savings, improved product quality, and shorter product launch times.
Book a DfM session at the best price
The key to successful DfM implementation is to start early, involve both the product development team and the manufacturing parts in the process, test and optimize the design, and get support from experts in the topic.
Book a DfM session by sending us an email today and improve your chances of getting a product ready for production with less time and money risk. Avoid getting an endless chain of confusing emails and possible misunderstandings by ensuring your design is perfectly fitted for your selected manufacturing process, whether 3D printing, CNC machining, Sheet Metal Fabrication, or Injection Molding.
Wikifactory is a trusted online, on-demand, and agile manufacturing platform supporting designers, engineers, and companies worldwide to produce their parts and products with our quality-assured manufacturing network with worldwide delivery. We are here to help you achieve all of your product development goals.
Get the latest articles on your inbox