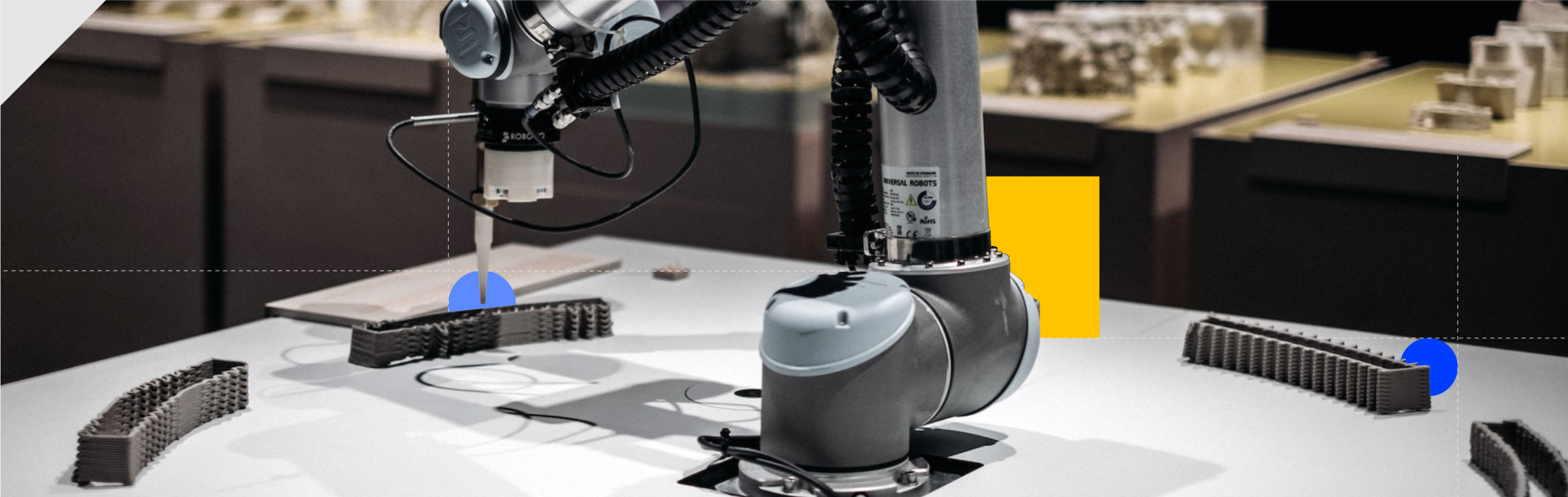
Manufacturing
Advanced materials, IoT, AI and more
Jan 11, 2023
It is important for businesses in the manufacturing industry to stay current with trends and changes in order to be successful and competitive. The manufacturing industry is always changing with new technologies and ideas that can help a company become more efficient, productive, and competitive, and create new opportunities for growth and innovation.
Ignoring or failing to keep up with these trends can leave companies behind their competitors and unable to leverage the benefits of new technologies fully while making it difficult for them to respond to changing customer needs and market conditions.
To stay competitive and take full advantage of the trending opportunities in the manufacturing industry, companies need to keep up-to-date with the latest developments and be willing to embrace new technologies and innovations as they emerge. Making the necessary changes and adopting the technologies most relevant to each company can involve Investing in research and development, training employees on new technologies, and collaborating with industry partners.
Manufacturing Trends in 2023
While it is impossible to predict with 100% accuracy the specific innovations and trends that will shape the most the manufacturing industry in 2023 as many factors can influence the direction of technological development, based on current trends and predictions here are some areas to pay attention over the next months:
1. Advanced robotics and artificial intelligence
Advanced robotics and artificial intelligence (AI) refers to highly developed and sophisticated robots and AI systems. These technologies allow for the automation of tasks and the optimization of manufacturing processes through machine learning algorithms.
Advanced robotics and AI in manufacturing can increase efficiency and productivity by automating repetitive processes or those requiring a high degree of precision, also improving the quality of products by reducing the potential for human error. Effectively adopting this trend can lead to cost savings by reducing the need for labor and materials.
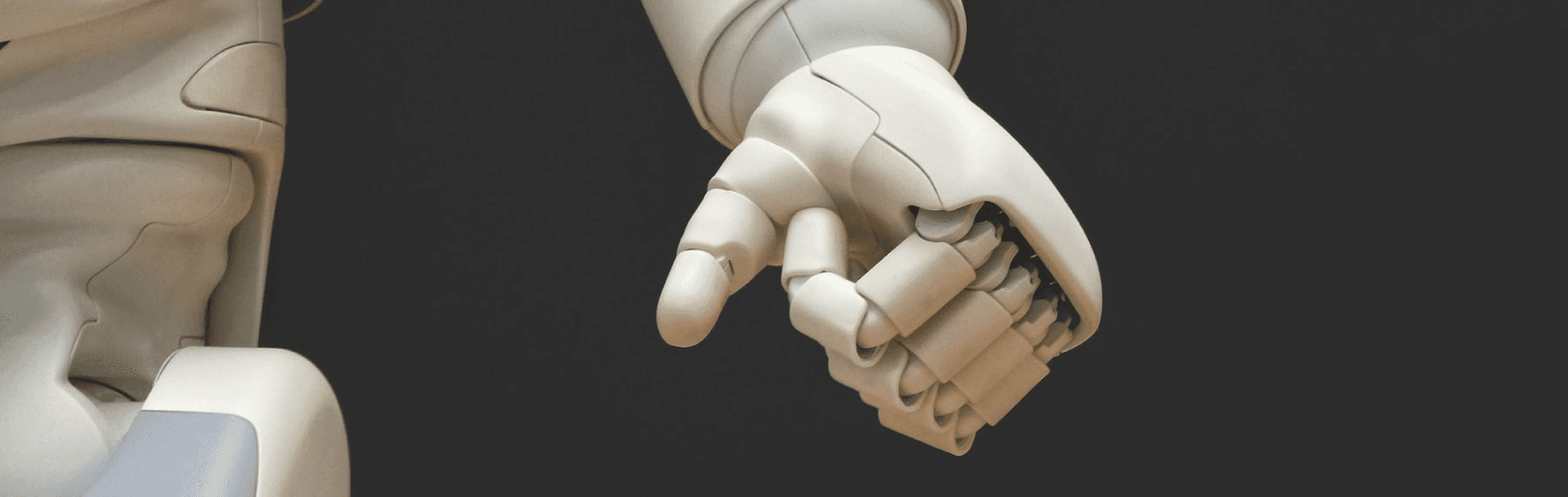
2. Internet of Things (IoT)
The Internet of Things or IoT involves using devices, such as sensors, actuators, and appliances connected to the internet, to collect and exchange data, allowing them to communicate and interact with each other.
The IoT will be trending thanks to its promising capacity to improve the efficiency and productivity of manufacturing processes by allowing for the real-time monitoring and control of equipment and resources. It can also enable the optimization of supply chain management and logistics through the use of connected devices. The adoption of IoT can improve the quality of products by allowing for the continuous monitoring of production processes and the early detection of defects.
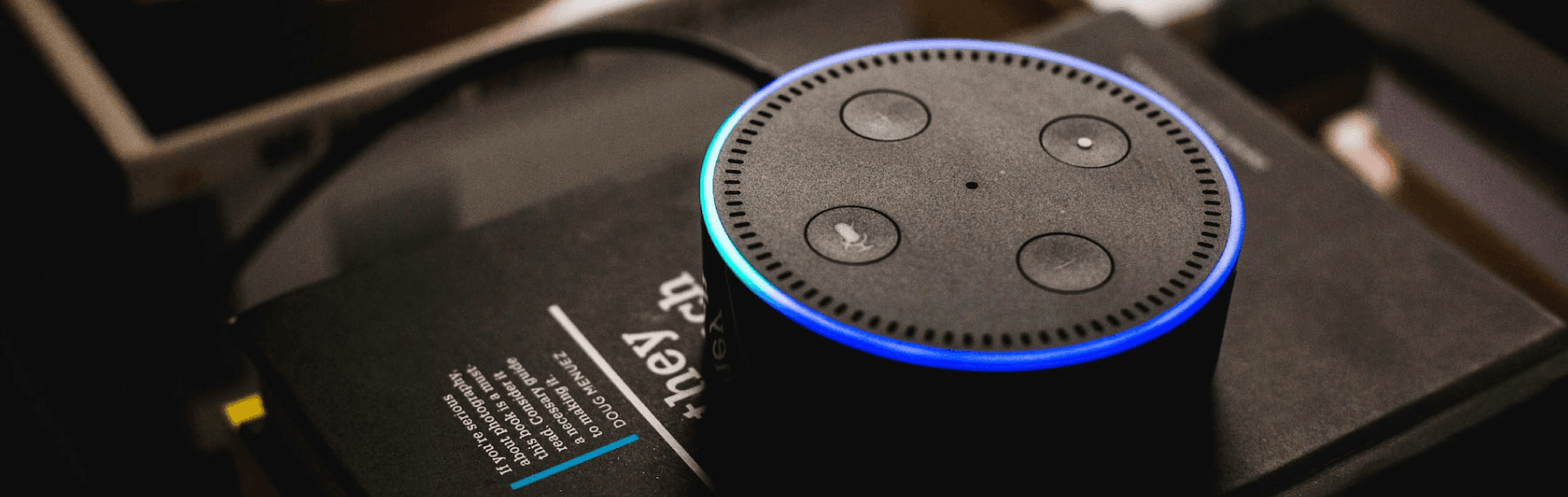
3. Additive manufacturing
Additive manufacturing, mostly known through 3D printing, creates a physical object by building it layer by layer from a digital model. It involves using specialized machines to fabricate objects from various materials, such as plastics, metals, and composites.
Additive manufacturing is expected to be a trend because it offers several benefits. For example, it allows for high-precision customized and complex parts. It also enables the rapid prototyping of new designs, which can help speed up development and innovation. Additionally, additive manufacturing can save costs by reducing the need for expensive tooling and production setup.
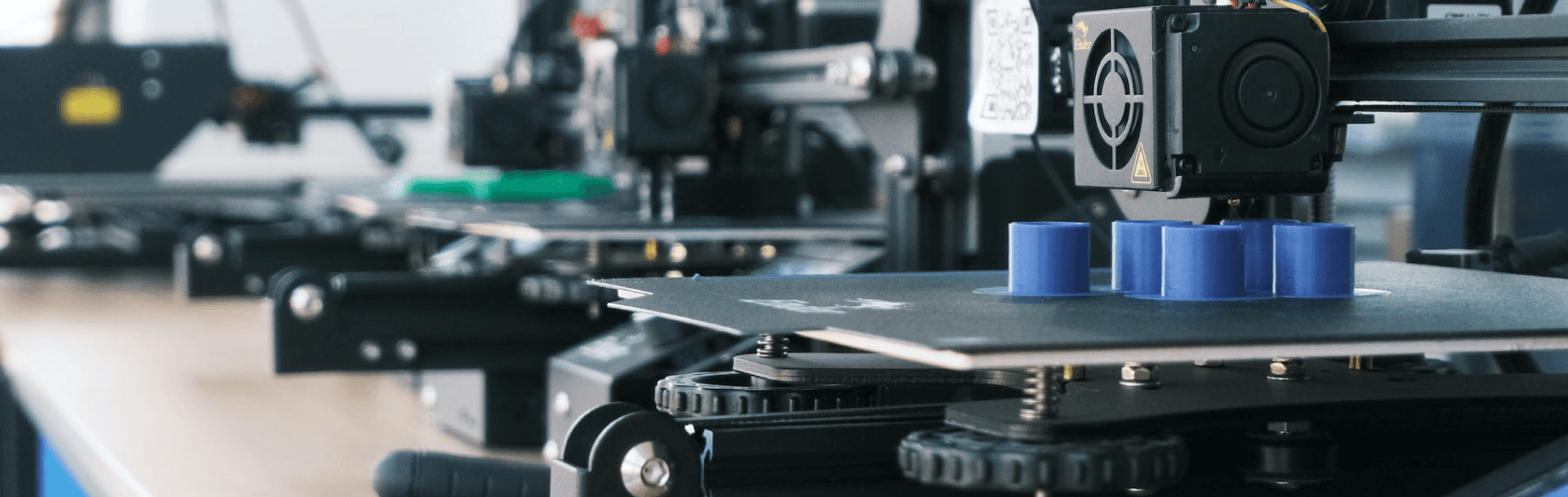
4. Advanced materials
Advanced materials refer to materials that have enhanced physical, chemical, or biological properties compared to traditional materials. Cutting-edge technologies such as nanotechnology, biotechnology, and materials science are used to create these materials.
The characteristic properties of these materials, such as high strength, durability, and corrosion resistance, can improve the performance and lifespan of products. They can also enable the production of lightweight and compact products, which can benefit transportation and energy efficiency. Advanced materials trends also respond to the possibility of developing new and innovative products that are not possible with traditional materials.
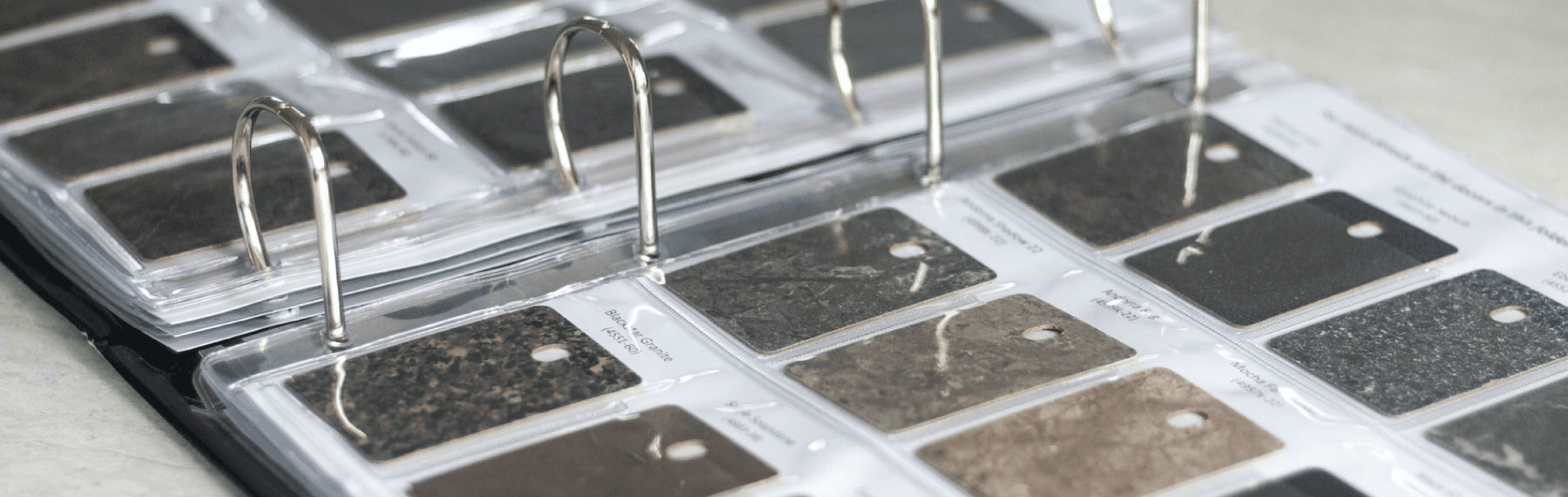
5. Industry 4.0
Industry 4.0, also known as the fourth industrial revolution, involves integrating advanced technologies like the Internet of Things (IoT), artificial intelligence (AI), and advanced robotics into manufacturing. These technologies enable manufacturing processes' automation and optimization through data analytics and machine learning algorithms.
Industry 4.0 will be a trending topic during 2023 thanks to its capacity to increase efficiency and productivity by allowing real-time monitoring and control of equipment and resources while enabling personalized product customization and mass production through data-driven decision-making. The fourth industrial revolution is already improving manufacturing processes' resource efficiency through smart technologies and will continue to do so.
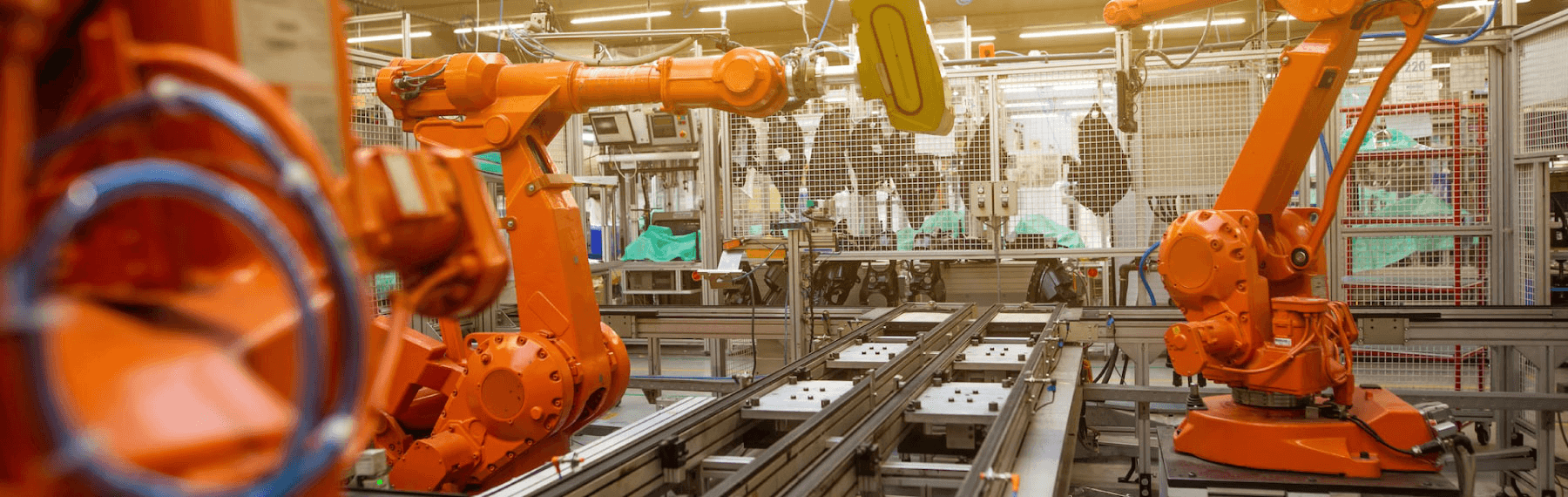
6. Sustainability and Circular Economy
Sustainability is the practice of using resources responsively to meet present needs without compromising the availability of such resources in the future for others. A circular economy is an economic model in which waste and resource depletion are minimized through using renewable resources and the reuse and recycling of materials.
The adoption of sustainability and circular economy principles in manufacturing looks to reduce the environmental impact of manufacturing processes by minimizing waste and resource depletion. It can also lead to cost savings by reducing the need for raw materials and resources. Adopting sustainability and circular economy principles can help businesses improve their reputation and meet the growing demand for environmentally-friendly products.
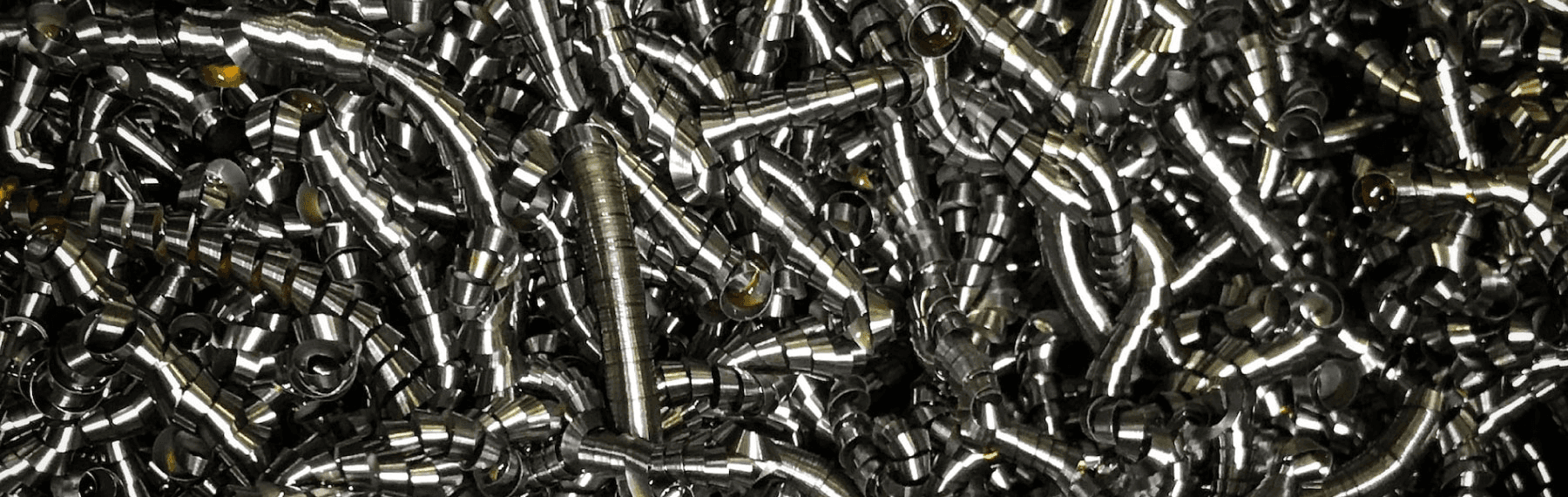
7. Advanced process control
Advanced process control uses algorithms and technologies, like data analytics, AI, and machine learning, to optimize and control manufacturing processes in real-time.
Adopting such processes can increase efficiency and productivity in manufacturing processes by allowing for real-time monitoring and control of equipment and resources. This process boosts a company's capacity to develop personalized product customization and mass production through data-driven decision-making. Another benefit is the improved quality and consistency of products by detecting and correcting defects in real-time.
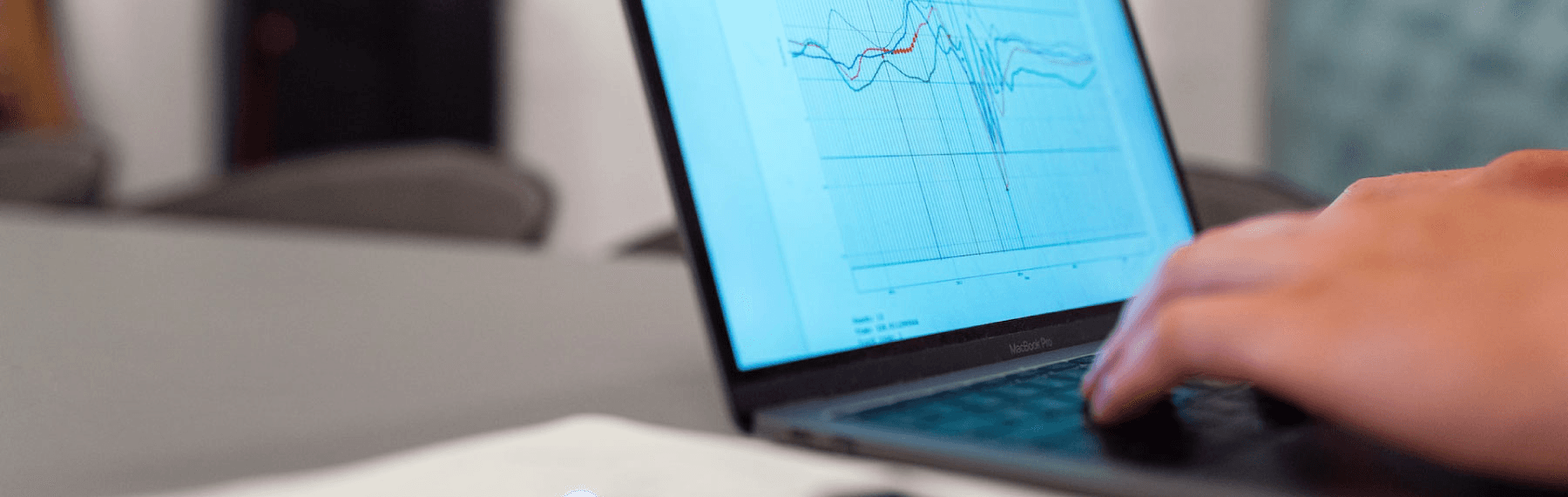
8. Predictive maintenance
Predictive maintenance use data analytics and machine learning algorithms to predict maintenance needs and equipment failures before they happen. This data allows for the proactive scheduling of maintenance tasks rather than relying on reactive maintenance when equipment breaks down.
In manufacturing, it can increase the efficiency and productivity of processes by reducing the downtime caused by equipment failures. At the same time, it also improves equipment safety by identifying and addressing potential issues before they occur, saving costs by reducing the need for reactive maintenance and the associated expenses.
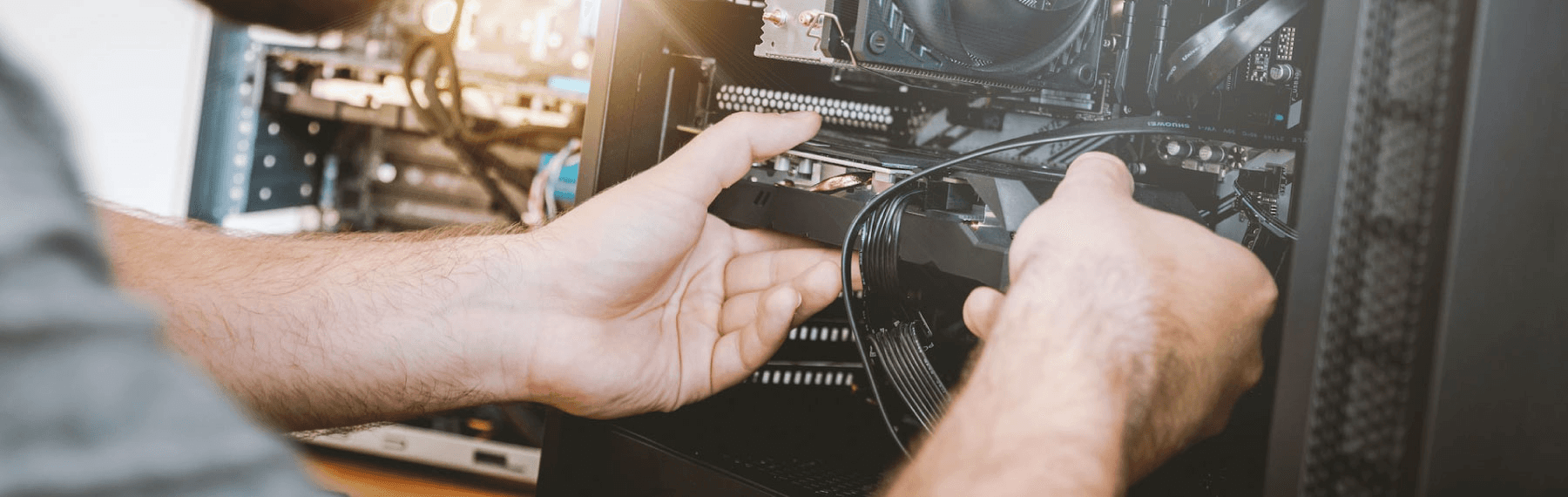
9. Collaborative robots
Collaborative robots, also known as cobots, are designed to work safely alongside humans. They can perform assembly, inspection, and transportation tasks in manufacturing environments.
Collaborative robots can improve manufacturing processes' efficiency and productivity by taking care of repetitive tasks or those requiring high precision. They can also help reduce the strain on human workers by performing physically demanding or hazardous tasks.
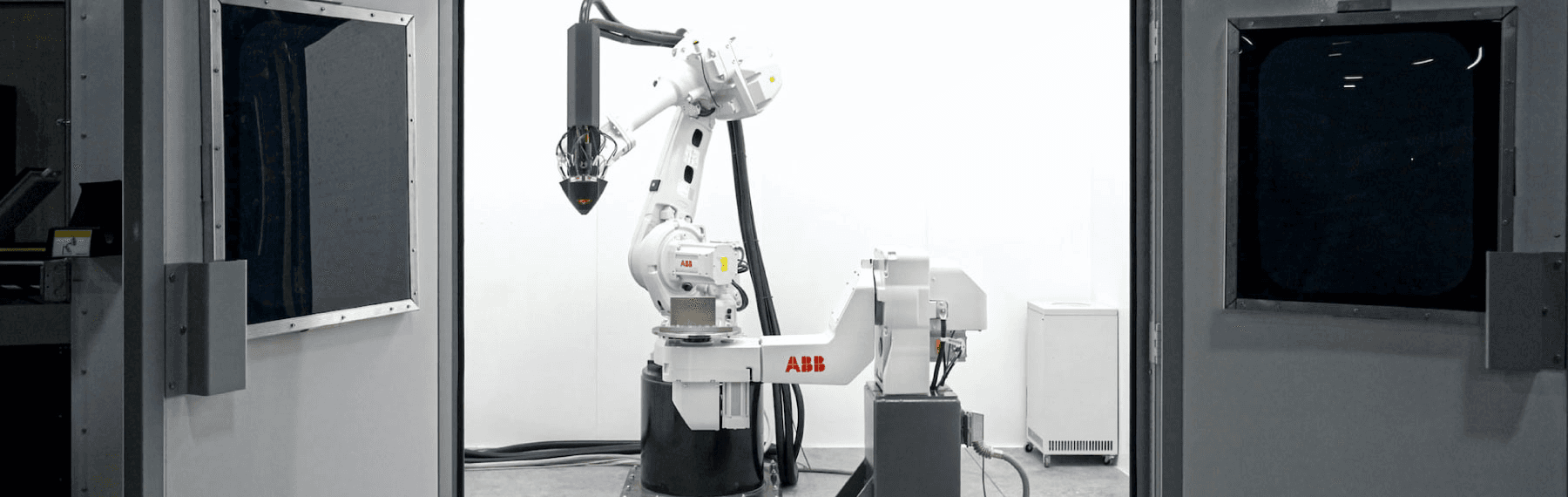
10. Digital twin technologies
Digital twin technologies are virtual models of physical assets, processes, and systems. These virtual models, also known as digital twins, are used to simulate and analyze the performance and behavior of their physical counterparts in a virtual environment.
Adopting digital twin technologies in manufacturing is expected to trend soon because of its benefits. They improve the efficiency and productivity of manufacturing processes by allowing for the virtual testing and optimization of designs, processes, and systems while also helping reduce the cost and risk of prototyping and testing by simulating them virtually. Besides, digital twin technologies can remotely monitor and manage physical assets, processes, and systems through sensors and other connected devices.
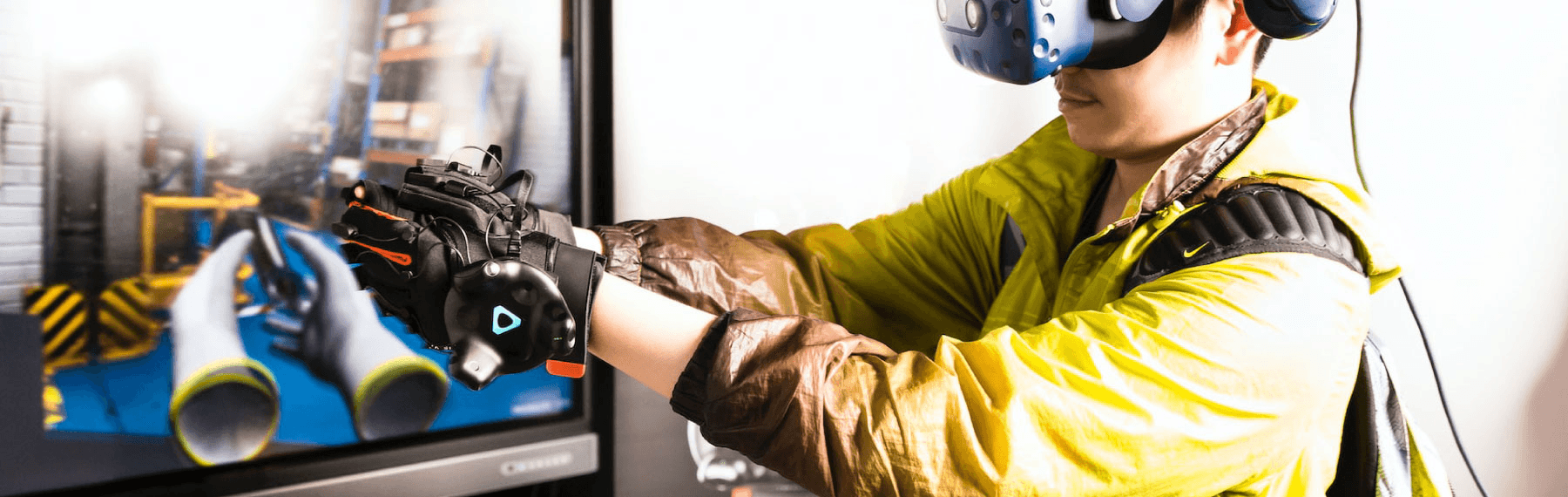
Stay ahead of your competitors
Staying up-to-date is critical for the success and competitiveness of companies in the sector. From advanced robotics and artificial intelligence to the Internet of Things and additive manufacturing, the trends we have explored in this article have the potential to bring significant benefits to the industry and drive progress.
Ignoring or failing to keep up with these trends can leave companies behind and unable to take advantage of the benefits. Companies need to take a step forward and embrace new technologies and innovations; otherwise, they risk falling short of their competitors and within the industry.
The future of Manufacturing and On-Demand Manufacturing
On-demand manufacturing is relevant to the manufacturing industry's future. It involves creating custom parts and products on demand rather than relying on significant, spacious inventories of finished goods or raw materials. The future of manufacturing must allow companies to respond more quickly to changing customer needs and market trends with cost-efficient and flexible supply chain systems.
Technologies like 3D printing or CNC machining are critical enablers of on-demand manufacturing and are shifting the way companies produce parts and products nowadays. These technologies can significantly benefit the manufacturing industry by allowing companies to create custom parts and products on demand and streamline production.
On-demand manufacturing represents a major innovation that can shape the industry's future and bring new efficiencies to the production process. Companies that embrace and leverage this approach will be well-positioned to succeed in an increasingly competitive global market.
Get the latest articles on your inbox