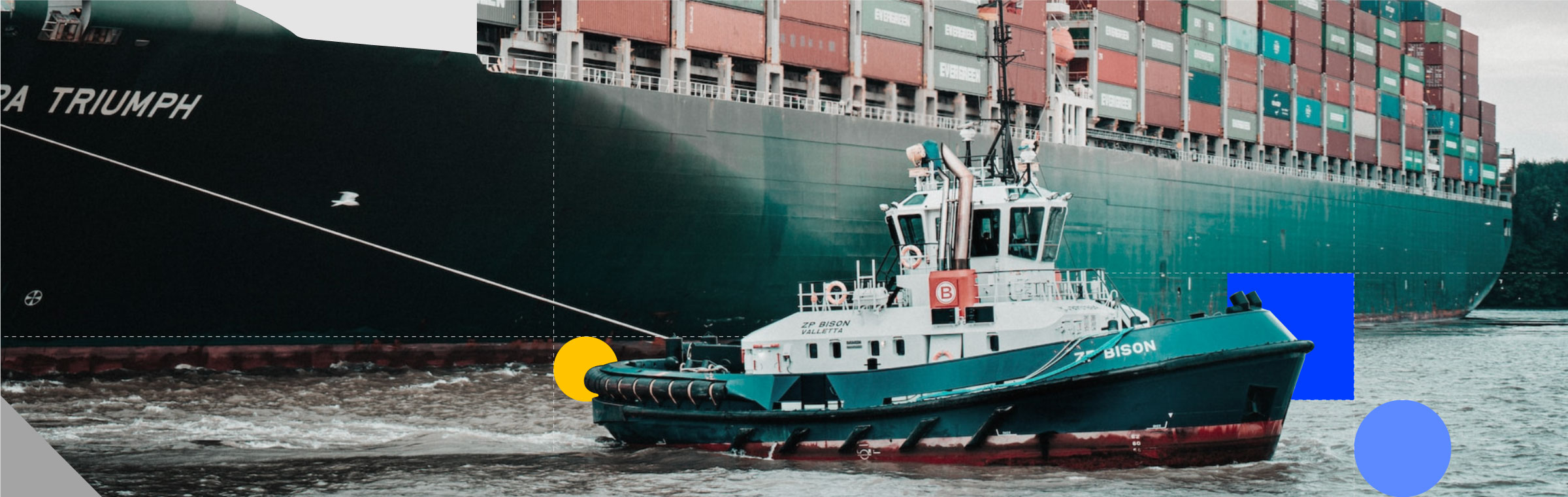
Supply Chain
Supply chain disruptions can happen anytime. Here's how to be prepared.
Jan 18, 2023
The global supply chain, which had a total trade value of $18.9 trillion in 2019, according to the World Trade Organization (WTO), has become more complex in recent years. Often, goods and materials travel long distances and pass through multiple countries before reaching their final destination.
While this has led to increased efficiency and lower costs, it has also made the supply chain more vulnerable to disruptions, with procurement and supply-chain professionals needing to stay constantly alert. Natural disasters, pandemics, political instability, and other factors can all impact the functioning of the supply chain, leading to delays, shortages, and other problems.
Stress testing has gained relevance for companies to mitigate the consequences of possible disruptions, which can lead to lost revenue, damage to reputation, and other adverse outcomes.
Keep reading to discover why Wikifactory is your biggest ally in building a resilient supply chain, prepared for potential disruptions.
What is stress testing?
Stress-testing a supply chain is like running a fire drill for your business. Imagine a fire breaking out in your warehouse. Do you have a plan in place to evacuate your employees safely? Do you have a backup plan for storing your inventory if the warehouse is damaged?
Stress-testing your supply chain helps you answer these types of questions and more by simulating various types of disruptions and analyzing the vulnerabilities and risks of your supply network.
By identifying potential problems through this process and developing strategies to mitigate them, you are preparing your business for success.
Just like a fire drill helps to ensure the safety of your employees and protect your assets, stress-testing your supply chain can help to safeguard your business and keep it running smoothly, no matter what challenges come your way.
How does stress testing work?
By stress-testing, companies can identify potential problems and develop strategies to mitigate them, improving their preparedness and resilience in the face of unexpected challenges. Here’s what it involves:
Identify potential sources of disruption
The first step in stress-testing a supply chain is identifying disorders that could impact it, including natural disasters, pandemics, political instability, or other factors.
Analyze the vulnerabilities and risks
Next, you should analyze your supply chain processes to identify vulnerabilities and assess the risks associated with disruptions, examining the locations of critical suppliers and distribution centers, the modes of transportation used, and other factors.
Develop contingency plans and backup solutions
Based on your supply chain operations analysis, you should develop contingency plans and backup solutions to mitigate identified risks. These include alternative suppliers, backup transportation options, or other strategies.
Implement and regularly review the stress-testing process
The stress-testing process should be implemented and regularly reviewed to ensure that your supply chain is as resilient and prepared as possible. For example, this might involve updating contingency plans as needed, conducting additional stress tests, or changing your traditional supply chain to improve its resilience.
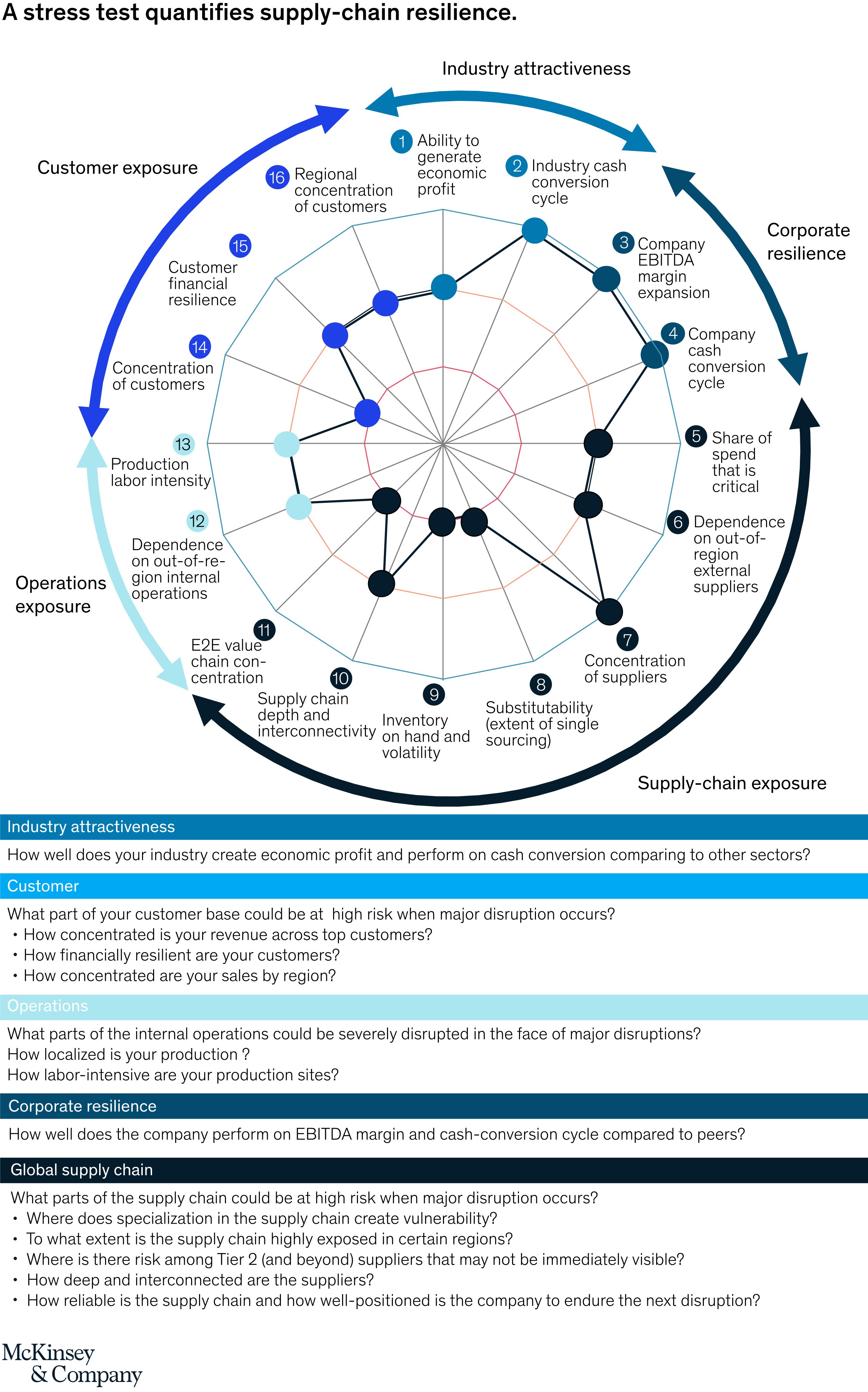
The global supply chain and the pandemic
The COVID-19 pandemic significantly impacted the worldwide supply chain. The sudden and widespread nature of the pandemic led to unprecedented problems related to the transportation, production, and distribution of goods, especially in the most affected areas.
Lockdowns and other measures to control the spread of the virus forced several factories to shut down or operate at reduced capacity, impacting production systems. In addition, travel restrictions implemented by numerous countries made it difficult for companies to transport the products between countries.
The pandemic highlighted the importance of stress-testing more than ever and having contingency plans to prepare for unexpected disruptions. It also demonstrated the need for businesses to be flexible and adaptable to continue operating in the face of challenges.
The risks of supply chain disruptions
Unprepared companies are more likely to suffer the consequences of unexpected disruptions. Supply chain problems can result in money loss and internal conflicts that may compromise a company’s operations:
Lost revenue: 90% of companies experienced supply chain difficulties due to COVID-19, resulting in an average loss of 26% of revenue, according to a survey by the Global Risk Institute. This loss of income can significantly impact a company’s bottom line.
Damage to reputation: Disruptions can lead to delays in the delivery of products and services, resulting in customer dissatisfaction and damaging a company’s reputation. Businesses that rely on customer loyalty, such as those in the retail or service sectors, might be affected the most.
Increased costs: In the event of supply shortages, businesses may have to spend more money on emergency measures, such as air freight or expedited orders, to minimize the impact of the interruption - leading to higher costs and reduced profitability.
Inefficient operations: In this scenario, companies need help to meet customer needs and maintain efficient operations, leading to inefficiencies and higher costs.
Internal stress: When an unprepared company is hit on its supply chain, failing to deliver on time and quality to its customers can result in colossal stress compromising its internal operations.
Mitigating Disruption Risks
There are several actions that companies can take in the short term to reduce the risks. These may include:
Increasing safety stocks of vulnerable parts.
Modifying contract terms to ensure the financial security of critical partners.
Investing in new skills and capabilities, such as adopting digital tools to improve supply chain visibility and provide early warning of potential problems.
Test on-demand manufacturing and evaluate its benefits compared to traditional manufacturing
In the medium to long term, companies can consider the following:
Diversifying their supply base.
Location diversification.
Vertical integration to reduce reliance on single suppliers.
Automation and digitization in manufacturing to increase production agility.
Additionally, companies can consider revising product designs to optimize complexity or reduce dependence on specialized components with limited availability.
Building a Risk-proof Supply Chain
Technology and data analytics is increasing in the global supply chain, with many companies adopting digital platforms and tools to optimize their operations. According to a report by McKinsey & Company, digitalization has the potential to increase global supply chain efficiency by up to 30%.
Build a more resilient, risk-proof supply chain model with Wikifactory. With our online, on-demand manufacturing services and design for manufacturing (DfM) support, Wikifactory can help optimize your supply chain and reduce reliance on single suppliers.
Leveraging advanced technologies such as CNC machining and Sheet Metal Fabrication, Wikifactory can help you increase production agility and reduce lead times, allowing you to adapt quickly to changing market conditions. Additionally, our platform will enable you to connect with a global network of manufacturers and access a wide range of materials and production capabilities, allowing you to source the products you need from anywhere in the world.
Try Wikifactory’s online, on-demand manufacturing services and DfM support today and take the first step into building a risk-proof supply chain. If you need more personal guidance, don't hesitate to contact us here, and we'll get in touch with you very soon.
Get the latest articles on your inbox