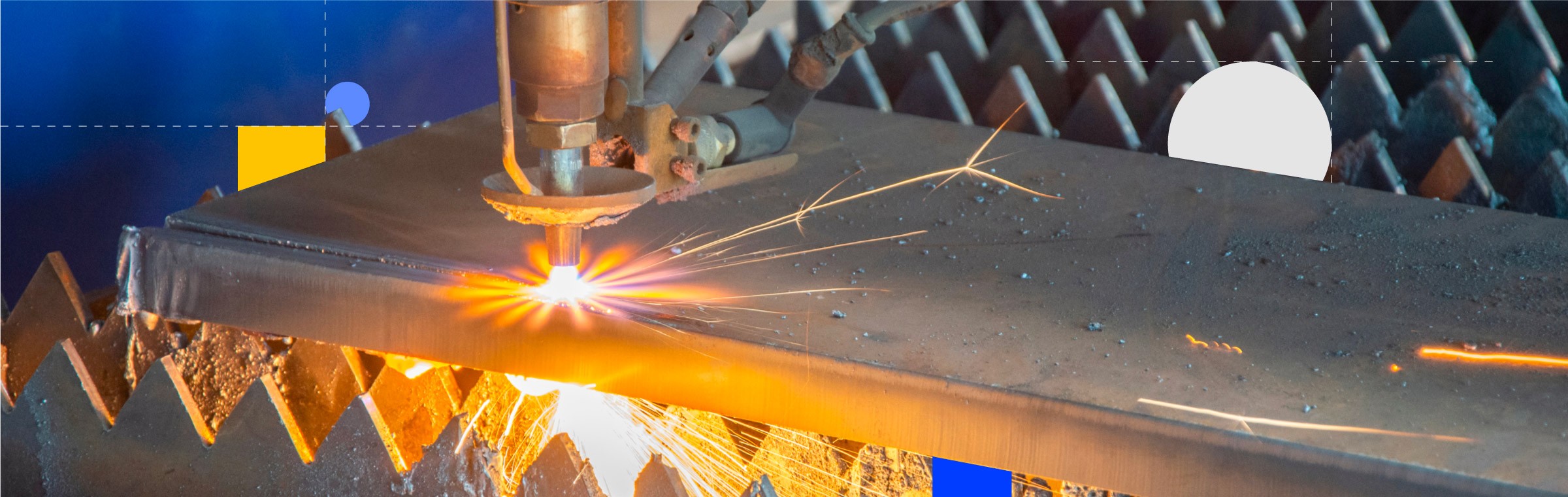
Sheet Metal Fabrication
Discover what Plasma Cutting can offer you
Dec 15, 2022
Plasma cutting is a Sheet Metal Fabrication process used to cut metal pieces into custom shapes. It is one of the most used metal-cutting methods in the manufacturing industry, and it’s categorized within the thermal cutting group as opposed to the mechanical cutting group.
How does a plasma cutter work?
The plasma cutter works by creating an energy-gas reaction that superheats gas up to 20,000 degrees, turning it into plasma, which is then directed via a nozzle at the workpiece to cut it.
The nozzle is operated with a CNC machine to ensure the highest precision in your parts and products.

Types of Plasma Cutting
Depending on how the plasma arc is created, there are different plasma-cutting processes:
High-frequency Contact Method
When the plasma torch makes contact with the metal sheet, a spark is produced, creating the plasma used to cut.
CNC cutters can’t use this process since this technique’s high voltage and high-frequency sparks can damage the machinery. Because of this, It is the least expensive and least precise plasma-cutting option.
Pilot Arc Method
A high voltage and low current circuit inside the torch first produces the spark, which creates the pilot arc. When the pilot arc comes into contact with the workpiece, the cutting arc is formed, and the cut process begins.
This process can be performed with CNC machines, making it more precise.
What materials can be cut with plasma?
Since plasma cutting relies on the reaction between the spark and the metal sheet, it can only be used to cut metals. Some of the materials that can be cut with this process are:
Steel
Stainless Steel
Aluminum
Copper
Brass
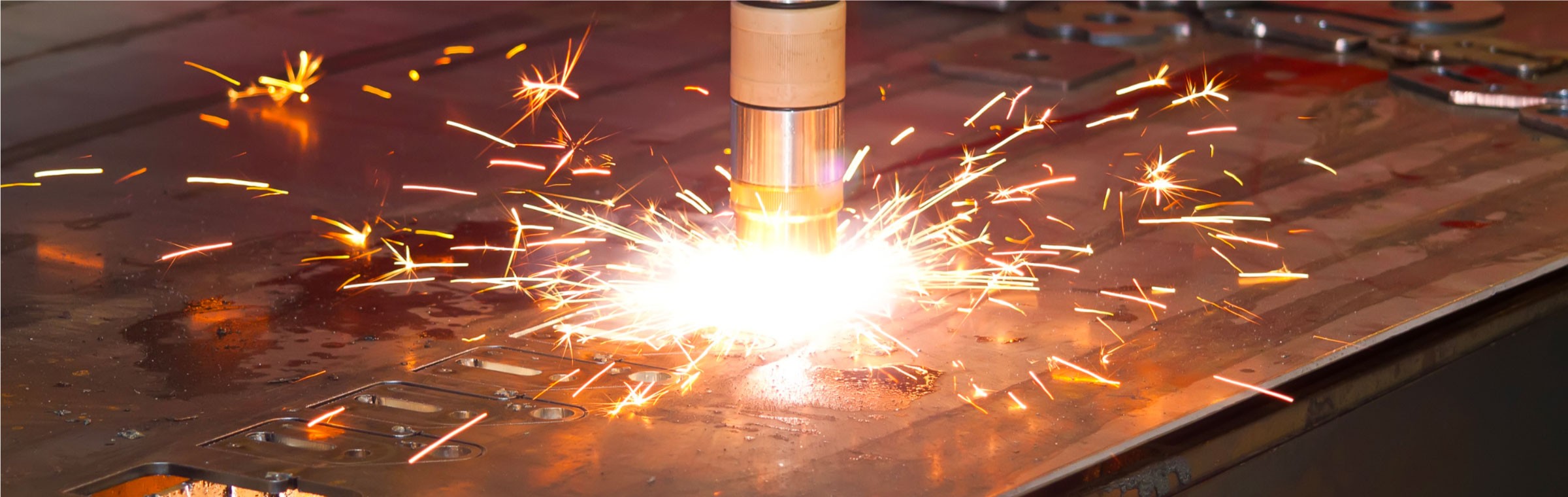
Benefits and Limitations of Plasma Cutting
One of its biggest advantages is the possibility to cut thicker metal sheets compared to other methods like Laser Cutting. The required metal thickness can be up to 300 mm for aluminum or 200 mm for steel, making it possible to create robust pieces, which is especially important for some industries. It is particularly cost-effective compared with laser or waterjet cutting.
On the other hand, the most significant disadvantage is the lower precision natural to the melting process involved, rougher finishings that may require a post-processing treatment, and possible warping problems due to the heat involved in the process.
Post-processing and finishings for Plasma Cutting
After plasma cutting, some of the following post-processing or finishing processes are commonly used to improve the part’s appearance and functionality.
Deburring
Edge dressing
Bending or forming
Welding
Painting
Anodizing, plating, polishing, and bead blasting are other common processes. The applied processes will depend on the specific requirements of your project.
Plasma Cutting Manufacturing with support and great costs
Get the best plasma cutting for sheet metal fabrication results by getting the support of expert engineers to produce your parts and products with the best quality and price.
Request a quote with Wikifactory and access a network of quality-assured manufacturers.
Get the latest articles on your inbox