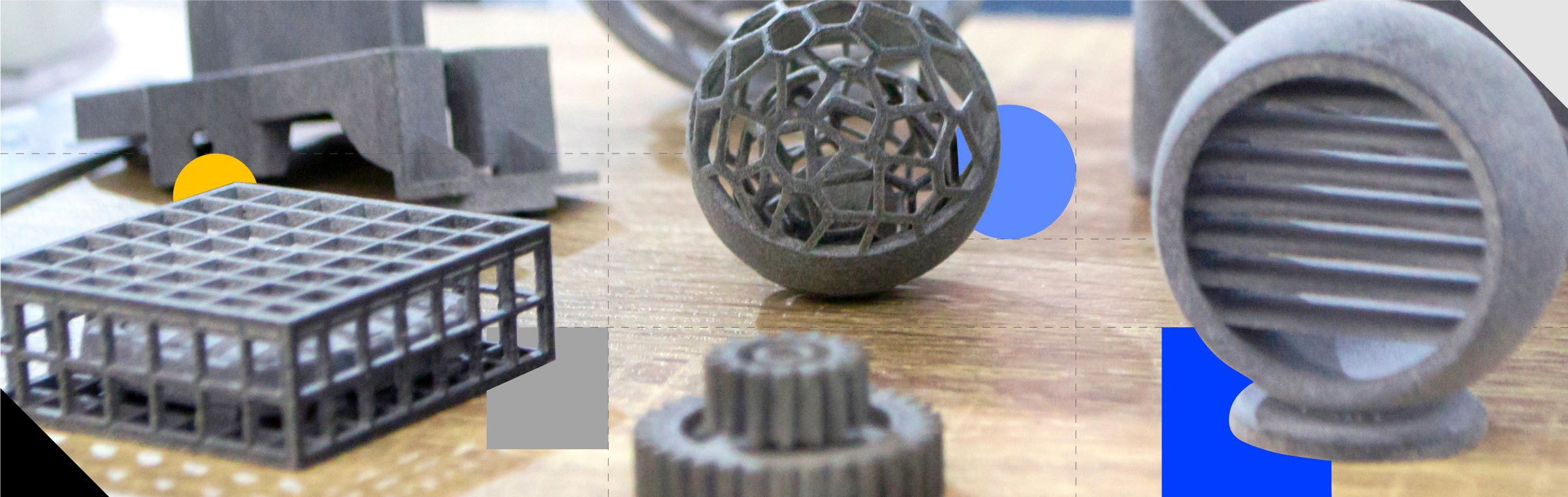
Design For Manufacturing
Reduce your manufacturing costs with Design for Manufacturing
Feb 7, 2023
Manufacturing a product can seem costly and complex at first glance, but getting the proper support in the process can make it very straightforward. A frequent doubt among many designers, engineers, and supply chain managers is how well-suited their design is before sending it to production.
Design for Manufacturing (DfM) is key to reducing time and costs effectively. Once you have read this article and fully understand DfM and its saving capacities, you will want to include it in your product development.
DfM is a methodology that involves designing products with the manufacturing process in mind to optimize efficiency, reduce spending and improve product quality. It is a holistic approach that considers all aspects of the product's design, production, and assembly to ensure that the final product is easy to manufacture, assemble and test.
Keep reading to learn how DfM can help you and your company cut manufacturing costs by designing more efficient products; then, get ready to send your products to manufacturing easily.
DfM and Cost Savings
One of the main benefits of DfM we will be exploring here is that it can lead to significant cost reduction during manufacturing. The process becomes more efficient by designing parts and products with the outcome and fabrication process in mind from the beginning.
Producing parts and products with manufacturing qualities in mind make them as easy and cost-effective as possible. At the same time, manufacturers can improve the efficiency of their operations, reduce waste, and increase the quality of your products, spending time in producing instead of fixing product design-related issues.
One of the key ways that DfM leads to cost savings is by using standard components. A standard component is a part or piece with standard measurements used repeatedly in an assembly or different elements. Using them across multiple products allows you to take advantage of economies of scale, lowering tooling and material costs. Using repeatable pieces allow manufacturers to reduce labor costs.
Designing parts that are easy to handle and align in the production line can also lead to savings. Making parts easy to handle reduce manufacturers' time and effort to move and position them during manufacturing, improving the manufacturing process's overall efficiency.
Implementing DfM
Implementing DfM in a manufacturing process can seem messy and compromise the tight times that most business owners have in mind, but you can do it quickly and effectively with the right approach. The key to successful implementation is to involve all stakeholders, including engineers, designers, and suppliers.
By working together and getting feedback from every part of the group, the team can identify areas of the design in combination with the manufacturing process that can be improved through DfM and develop strategies to address these areas.
Design for Manufacturing Guide
Design for Manufacturing can significantly impact the success of a product in the market. Optimizing your product during the design stage before producing it can cut deficiencies while improving the quality and reliability of the product.
The following DfM guide provides a comprehensive and professional approach to implementing DfM, covering key considerations and steps designers and engineers like you can take to streamline the manufacturing process.
1. Define the objectives and goals of DfM
Start by determining what you hope to achieve through the DfM process. The objectives could include reducing overhead costs, improving quality, reducing lead time, or increasing production efficiency.
2. Assess the production process
Before putting your hands into the design phase, understand the manufacturing processes and technologies you will use to make your product. Doing so will inform and optimize the design for the intended manufacturing process.
3. Evaluate material options
Choose cost-effective, readily available, and suitable materials for the fabrication process. Consider the material's strength, durability, and ability to withstand production and intended use. Remember that quality makes a critical impact on customer satisfaction.
4. Design for ease of assembly
Analyze your product's assembly process and identify potential issues that could arise during it. Designing the product by thinking about its assembly will reduce production time, costs, and headaches.
5. Consider production requirements
Determine what equipment and tooling you will need and design accordingly. A well-suited design will minimize production time and consider the available technological capacity. Choose your supplier consequently and talk to them to understand their technical capabilities and needs. Close communication will ensure less time-consuming changes.
6. Evaluate the supply chain
Consider the entire supply chain, from raw materials to components and finished products. Evaluate the logistics of the supply chain and ensure that everything can be obtained and delivered on time.
7. Analyze the impact on the cost
Throughout the design process, keep track of the impact of the design adjustments on the production costs, which can become opportunities to reduce your budget in the long term.
8. Validate the design through prototypes
Don't jump straight into mass production. First, validate the design through prototypes and testing. Even though DfM will increase your chances of having a high-quality, hassle-free product, ensure that your design meets performance, reliability, and quality requirements by making prototypes.
9. Continuously improve
Regularly review and analyze the design and manufacturing processes to identify opportunities for improvement. Continuously evaluate the DfM process and make adjustments as needed to ensure that the product is optimized for manufacturing.
10. Get feedback from a DfM expert
A few specialized professionals working in the manufacturing industry offer DfM consultancy services. Booking a session with one of them will save you time and money in your product development process.
DFM to improve your Product Development Process
In conclusion, Design for Manufacturing is a powerful tool that can greatly impact the success of a product in the market. By considering manufacturing processes, materials, assembly methods, and other key factors in the design process, companies and entrepreneurs can reduce time and costs in their manufacturing processes while improving the quality and reliability of their products.
Implementing DfM is a smart and cost-effective way to improve your designs and streamline manufacturing, and you can get the most out of it by booking a DfM session with Wikifactory experts. You can design a product that is easy to manufacture, reduce production time, and cut part costs without sacrificing quality. Contact us here with an overview of your project and concerns, and we'll get in touch with you.
Reduce your manufacturing costs with DfM today and take your product designs to the next level! If you have any doubts, don't hesitate and leave your comments and feedback below.
Get the latest articles on your inbox