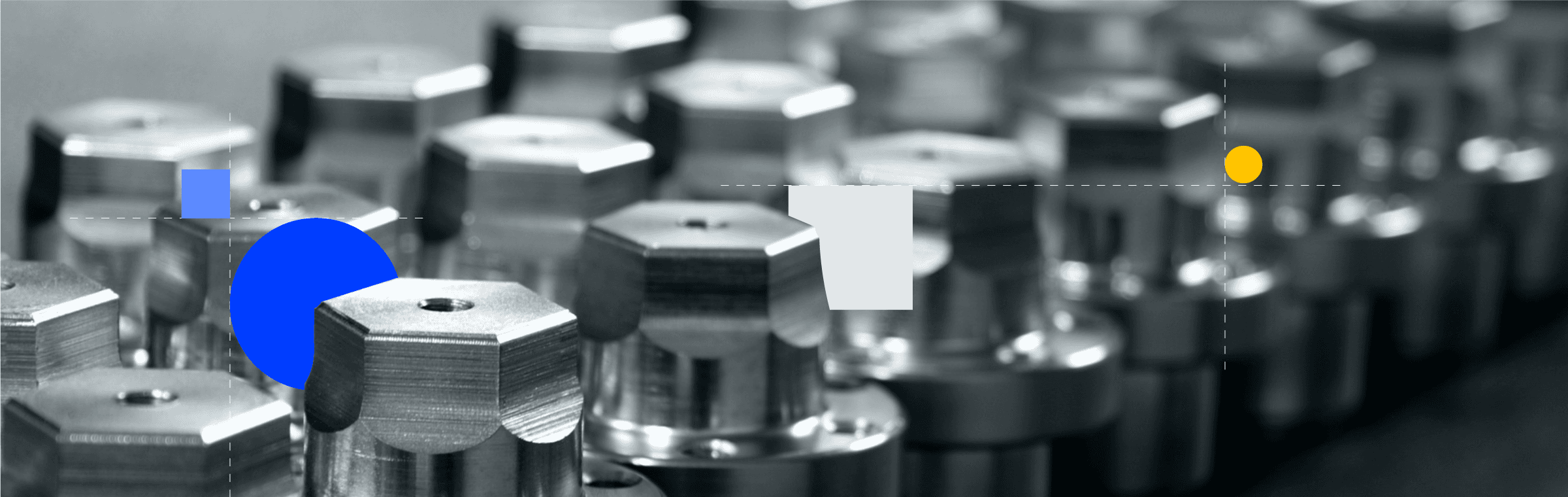
CNC Machining
High costs of CNC machining? Save money in manufacturing with us
Dec 23, 2022
CNC machining is a manufacturing process in which computer-controlled tools are used to cut and shape materials into precise shapes and dimensions, which is essential in today’s manufacturing industry. Its high precision and consistency make it highly valuable to many industries, such as aerospace, automotive, and medical. But how much does CNC machining cost?
Different factors affect the manufacturing costs of CNC machining. From the amount of manual labor required, and the needed machines, to the size and amount of product to be fabricated, pricing depends on many factors. Still, it ultimately can be one of the most cost-effective manufacturing processes.
What affects costs in CNC machining
Let’s dive in to analyze each pricing point and learn how to save money in manufacturing with CNC machining:
01 Material selection
The cost of CNC machining is heavily influenced by the type of material used. The material chosen for CNC machining must be suitable for the intended use and application and be able to withstand the stresses and forces applied during the manufacturing process.
The material must also be compatible with the machining process and the tools used, maintaining its dimensional stability and physical properties during and after the procedure.
Material selection impacts its cost and production time, whether stainless steel, plastic, or other. Inadequate material selection can result in costly delays, repairs, or even product failure. Therefore, careful consideration and evaluation of the material properties and requirements are essential to ensure the success of the CNC machining process.
Pro tip: choose your material carefully and based on your part’s needs. Some metals are more difficult to work with than others and cost may vary greatly from one choice to another.
02 Design Complexity
The more complex the product design, the more time and effort it takes to produce your CNC machined parts, which can increase the cost of the manufacturing process. Intricate designs often require specialized tools and techniques, adding to the overall cost. Complex designs may also require more material removal and machining time, which increases the cost.
Straightforward designs are generally easier and faster to produce, which can result in lower manufacturing costs. Therefore, balancing the product’s desired functionality and performance with the manufacturing process's cost-effectiveness is essential.
Pro tip: incorporate Design for Manufacturing or Assembly (DFMA) or Design for Cost (DFC) principles early in your product development process, starting from the design stage, and you will later benefit from lower costs, production time, and overall hassle.
03 Production Volume
The cost of CNC machining is generally calculated based on the time and effort required to produce a part and the cost of the materials and tools used. The larger the production volume, the lower the cost per part. This is because the setup and preparation costs are spread over more parts, reducing the overall cost.
However, it is essential to consider the economies of scale when determining the production volume. As the production volume increases, the cost per part may not decrease linearly. Carefully evaluate the production volume and cost per part to determine the most cost-effective manufacturing strategy.
Pro tip: the best way to know exactly how much your production batch will cost is by submitting an RFQ here and specifying the number of units you’d like to consider for your quote.
04 Precision
The precision of a part is determined by the accuracy and consistency of its dimensions and geometry. The higher the precision required for a part, the more time and effort it takes to produce it, which can increase the cost of the manufacturing process.
For example, producing a part with tight tolerances and high dimensional accuracy requires specialized tools and techniques and more precise machining operations. This can result in longer machining times and higher tool wear, which can increase the cost of the manufacturing process. On the other hand, producing a part with lower precision requirements may be faster and more cost-effective if such precision is not needed.
Evaluate the precision requirements of a part and determine the most cost-effective manufacturing strategy. In some cases, it may be necessary to compromise on precision to reduce the production process cost. In contrast, in other cases, the accuracy may be critical and must be prioritized.
Pro tip: DFMA guidance can be key in achieving precision, especially for inexperienced clients. When producing parts that need to be assembled, precision is not to be overlooked.
05 Manual Labor
The use of manual labor can increase the cost of production in several ways. For example, setup, files or material handling, and quality inspection can add to the overall labor cost. Manual labor is subject to variations in skill, experience, and hourly rate, which can impact the quality and consistency of the finished product.
Make sure your files are ready for production and your overall process is entirely automated so you need the least amount of labor.
Pro tip: Smart production starts with the design and requirements of a customer’s fabrication needs. Getting DFM support will significantly improve your design's feasibility before sending it to production, with considerable time and money savings.
06 Surface Finishings
A part’s surface finish refers to its surface’s texture and appearance, which can impact its performance and aesthetic appeal. The machining operations and techniques used, as well as the tools and materials used, depend entirely on your project’s needs.
The cost of surface finishing depends on the time and effort required to perform the machining operations to achieve the desired finish. Some finishes, such as polishing and plating, can be time-consuming and require specialized equipment, increasing the cost. On the other hand, other finishes, such as sandblasting and tumbling, can be faster and, therefore, less costly.
Pro tip: Carefully select the finishings that you need based on the final use that your part will have. Cut costs by avoiding including purely aesthetic finishings with little or no benefit to your part’s end use.
Costs in CNC machining
As you’ve seen, the cost of CNC machining manufacturing is influenced by several factors, including the type of material used, the complexity of the design, the number of parts being produced, and the precision required. To summarize, these factors are:
Material Selection
Design Complexity
Production Volume
Precision
Manual Labor
Surface Finishings
Benefits of CNC machining
Manufacturing with CNC machining has many benefits. Producing your parts and products with this fabrication process is an excellent option for those looking to produce in large batches and even in smaller numbers.
Get to know all about the advantages and disadvantages of CNC machining here.
Save money in manufacturing with CNC machining.
The best way of getting the best costs when manufacturing with CNC machining is to use a reliable manufacturing partner like Wikifactory. Get a quote with the best costs today and receive engineering and DFM support to get cost-saving ideas, access a network of quality-assured manufacturers, and worldwide delivery.
Get the latest articles on your inbox